PROCESS RECONCILIATIONS
By updating barcode/ QR code of each single item, rack and temporary container (including pallet, tote, cart), eton’s system creates accurate record on every step implemented on products.
For example: A cup was received into a tote labeled barcode 0101. Then this cup disappeared while worker brought the tote to racks for stowing. In this case, eton’s system updates that the cup was lost in transferring from inbound dock to racks.
When this cup is found in another process (still sellable, not damaged or defective), it will be automatically restored in inventory list.
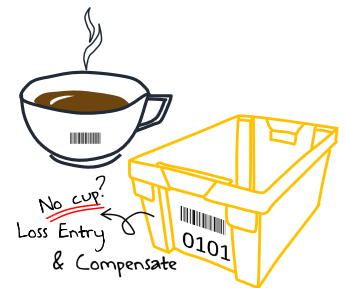
mismatch redution
Most of warehousing systems in Vietnam record only the number of items received, stored and shipped out of warehouse. Working with this recording method, workers have to remember clearly which SKU is located at which location. This is very difficult if we have a wide range of SKUs. Sometimes, it also results in wrong-picking, miss-picking while fulfilling a customer’s order.
Instead of that, eton’s workers are supported by an intelligent system, which can exactly suggest where the items are located and record which items are picked, packed and shipped. This helps to minimize picking time, keep track storage (including volume, location, expiration period) and optimize replenishment plan.
With eton’s system, pausing and counting all items in warehouse is unnecessary anymore. Because once an SKU is set “in counting”, system will list out all the locations containing that SKU. Worker’s task is simply coming to the locations, checking all the items (not only the “in counting” SKU but also other SKUs available in that location). This method helps to check storage every hour, every day and flag out mismatches between physical inventory and systematic data earlier.
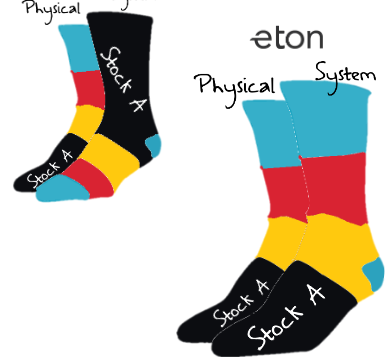
tracking 1,000s of sellers at once
eton’ system concatenates each product’s manufacturing barcode and PO (Purchase Order) barcode, then record it as a virtual unique ID (UID) on system instead of labelling a physical UID on an item. This helps to eliminate printing and labelling time, but still guarantee accurate tracking for each single PO and vendor on system.
Therefore, eton can support big brands or retailers to trace back information of products from different manufacturers or suppliers, respectively.
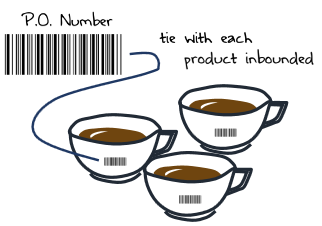
PICK-PATH OPTIMIZATION
To support workers in picking, eton’s system creates Pick Waves based on types of orders. A Pick Wave is divided into many Pick Lists containing the items to be picked. Pick List can include an order or many orders, an SKUs or many SKUs; depending on the number of items in the orders.
The system also calculates and finds out the shortest picking path, then suggests one by one locations on mobile device so that workers can walk along that direction without thinking.
eton Tech team continuously analyses data and optimize AI rules for minimizing picking path and processing time over all ranges of dimensions, products.
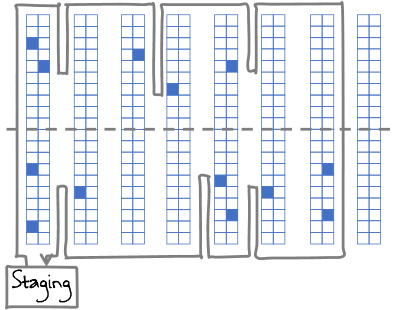
API CONNECTION
When clients set up API connection with eton, order information from their websites is synchronized into eton’s system on a nearly real time basis. Hence, eton can handle those orders in the shortest lead time and the highest accuracy.
On the other hand, API connection also helps eton to share our inventory information to each client in our system, both manufacturers outsourced by international brands and retailers.
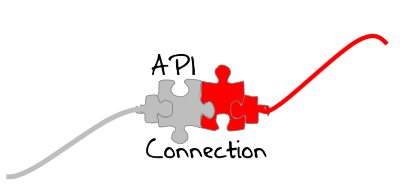
AGILE FLOWS
The combination between an intelligent system and a fine-tuned physical process is the reason behind eton’s firm confidence in handling a wide range of product specifications and dimensions. Hence, we can ensure to provide the best Fulfillment service to every client.
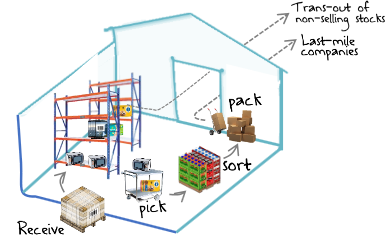
step by step fulfillment service
eton’s Fulfillment system and process strongly prevail upon other systems all over Vietnam. These advantages show up via every single item’s movement in warehouse: receiving, stowing onto rack, picking, sorting multiple items into an order, packing and counting stored products.